Dive Into the Globe of Light Weight Aluminum Casting: Comprehending the Different Approaches
Light weight aluminum casting is a fundamental procedure in the production market, with various techniques used to create complex and specific components. Understanding the various techniques made use of in light weight aluminum casting can give useful insights right into the abilities and limitations of each strategy. From the conventional sand casting technique to the advanced die casting process, each technique offers one-of-a-kind advantages relying on the demands of the project. Exploring these diverse methods can use a detailed view of the opportunities within the globe of aluminum casting and just how each method adds to shaping the modern-day manufacturing landscape.
Sand Casting Approach
Sand spreading, a widely-used approach in light weight aluminum casting processes, involves creating mold and mildews made of compressed sand for putting liquified metal. When the mold is ready, it is securely positioned in a flask and molten light weight aluminum is poured into the dental caries.
After the steel has actually cooled and solidified, the sand mold and mildew is escaped to expose the aluminum spreading. Sand spreading permits the manufacturing of complicated shapes and huge components that may be challenging or expensive to create making use of other methods. It is additionally a lasting technique as the sand can be reused and utilized multiple times, reducing waste in the spreading process.
Permanent Mold Strategy
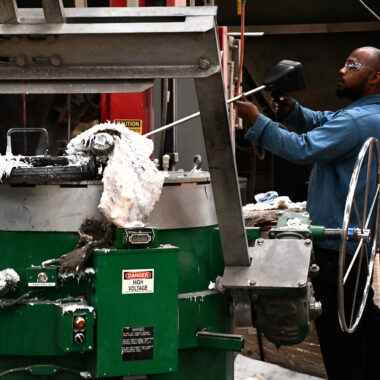
One significant advantage of the Permanent Mold Technique is the improved dimensional accuracy it offers. The steel mold and mildew permits tighter resistances and better information in the final light weight aluminum spreadings contrasted to sand spreading techniques. This precision makes it a favored option for applications where tight dimensional control is important, such as in the vehicle and aerospace markets.
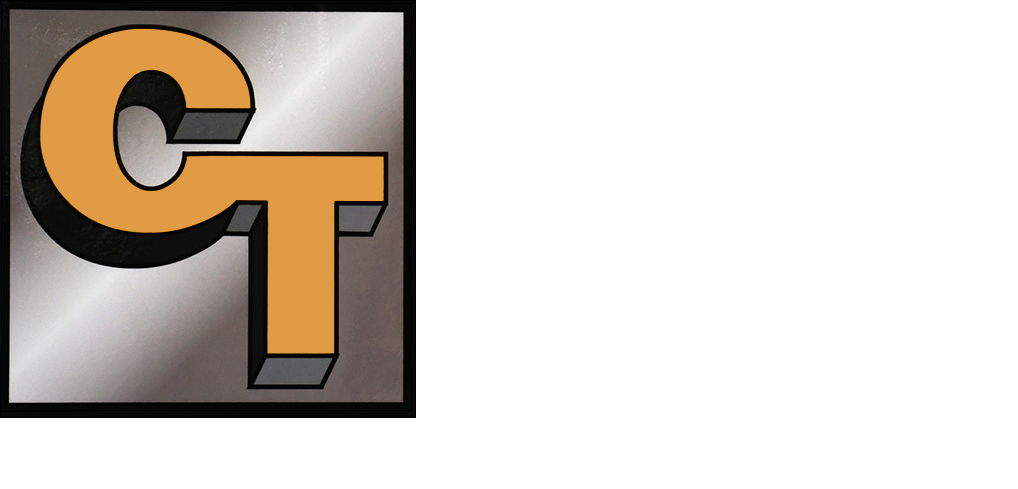
Pass Away Casting Process
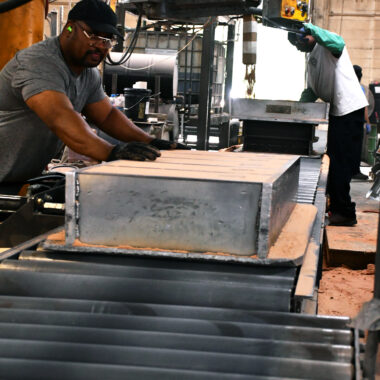
Financial Investment Casting Technique
Using a precision casting method, Financial investment Casting Strategy entails producing complex aluminum components by pouring liquified metal into a ceramic mold. This procedure, additionally called lost-wax casting, begins with the creation of a wax pattern of the wanted component. This wax pattern is then covered with a ceramic product to develop a shell. As soon as the ceramic covering is hardened, it is heated to get rid of the wax, leaving behind a hollow ceramic mold.
The next action includes putting the molten aluminum into the ceramic mold and mildew. The aluminum loads the tooth cavity left by the wax pattern, taking its shape exactly. This method is preferred for its ability to create complex forms with high precision and a smooth surface coating. Investment pop over to these guys spreading is commonly made use of for manufacturing elements in industries where tight resistances and intricate styles are called for, such as aerospace, automobile, and clinical tools. The adaptability and accuracy of the Investment Casting Technique make it a valuable method on the planet of aluminum spreading.
Lost Foam Casting Technique
Having explored the intricate precision of Financial investment Casting Strategy, the emphasis now moves to the innovative method of Lost Foam Casting in light weight aluminum part manufacturing. Lost Foam Casting, also recognized as evaporative pattern spreading, is a contemporary technique where a foam pattern of the desired component is produced and then covered with a refractory product.
One of the main benefits of Lost Foam Spreading is its ability to produce intricate shapes with elaborate information, often in a solitary piece without the need for added get redirected here machining. This technique is also recognized for its high dimensional precision and smooth surface coating. Furthermore, Lost Foam Spreading is a cost-efficient process as it decreases the need for cores and permits the production of light-weight browse around these guys elements. Despite its benefits, Lost Foam Casting needs careful control of the spreading process to protect against problems and ensure high quality parts.
Final Thought
To conclude, aluminum spreading supplies a variety of techniques such as sand spreading, permanent mold method, pass away spreading, investment casting, and lost foam spreading. Each approach has its own advantages and applications, making aluminum casting a functional and extensively used process in different markets. Recognizing the differences between these methods is vital in picking the most suitable casting technique for particular manufacturing demands.
Sand spreading, a widely-used approach in light weight aluminum spreading procedures, entails developing mold and mildews made of compressed sand for putting liquified steel. aluminum casting.The Irreversible Mold Technique, like sand casting, is another prevalent method employed in aluminum casting processes, offering distinct benefits in terms of mold and mildew reusability and dimensional precision. The steel mold allows for tighter tolerances and better information in the last light weight aluminum castings compared to sand casting approaches. The 2 major kinds of die casting are cold chamber pass away spreading and warm chamber die casting, each suitable for various kinds of light weight aluminum alloys.In final thought, aluminum spreading supplies a range of techniques such as sand casting, permanent mold and mildew method, die casting, investment casting, and shed foam spreading
Comments on “Unlocking Quality: Aluminum Casting Techniques & Tips for Superior Outcomes”